By Jason Spruell
Semiconductor Packaging is driving the More than Moore revolution and accelerating the development of ever-powerful electronics. In previous articles, we discussed how advanced polyimides are enabling this More than Moore revolution. Critical to these technologies are photosensitive polyimides.
Polyimides are used as redistribution layer (RDL) dielectrics in the most advanced semiconductor packaging applications enabling thinner, smaller, faster, and ever more integrated electronic devices. In addition to providing the required electrical, mechanical, and thermal properties for long-lived reliable packages, Photosensitive polyimides (PSPIs) must also be patternable at minute scales in order for the redistribution layers to be built-up efficiently. The design of these highly-engineered materials presents unique challenges that Halocarbon Polyimide Processing Agents can help to address. These commercially-viable processing technologies enable the efficient and scale production of next-generation RDL dielectric materials.
How are PSPIs Used?
Photosensitive materials are the backbone of the semiconductor industry. They change their solubility in response to irradiation – either becoming soluble or insoluble in a developer solution upon undergoing a chemical transformation that is catalyzed by exposure to light. Photosensitive polyimides are a special class of photosensitive materials that are patterned with light, developed, and then thermally cured to form the final material in a specific photo-defined area. This general process is shown in Figure 1 in which the PSPI precursor is crosslinked in the areas exposed to light (step 3) and subsequently cured-in-place (step 5) to form the polyimide.
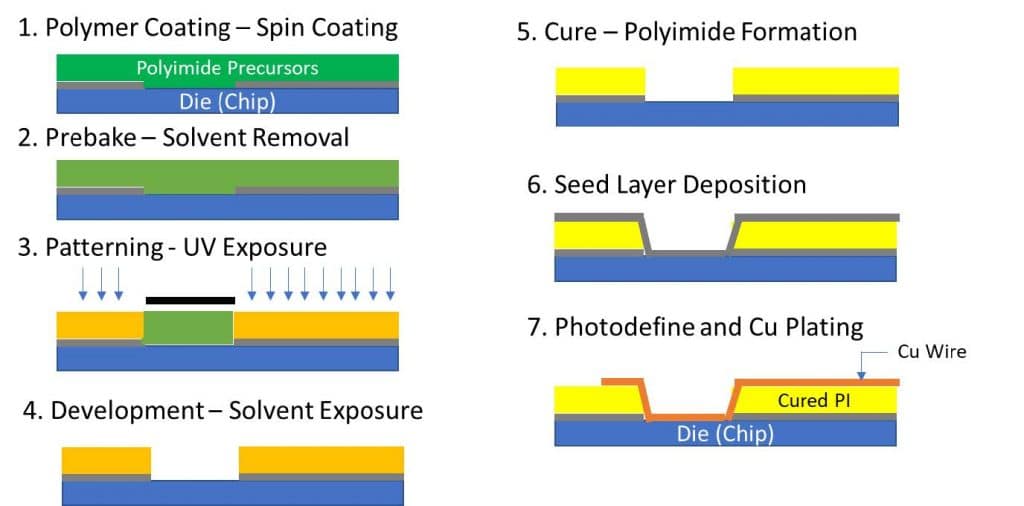
Figure 1. Photosensitive Polyimides in action whereby irradiation induces cross-linking of the polyimide precursor which is later thermally cured to form the redistribution layer dielectric (Negative tone PSPI displayed).
PSPIs are Polyamic Esters
Polyamic esters are critical to the function of PSPIs. The key chemical transformation leading to the permanent polyimide is the thermal rearrangement of polyamic esters to polyimides. This transformation results in the formation of the final polyimide through the elimination of the alcohol that was previously bound as an ester. Whether the PSPI is a negative tone or a positive tone material, this common polyamic ester intermediate is the critical structural element for effective PSPI manufacture (Figure 2).
For negative tone PSPI, crosslinking groups are incorporated through the ester groups of the polyamic ester. Upon irradiation in the presence of additional monomer, crosslinking reactions facilitate incorporation of the polyamic ester macromolecules into a larger polymer network. More importantly, the irradiated regions in a negative-tone PSPI are rendered insoluble because of this crosslinking. Upon curing, the polyamic ester bonds are cleaved, breaking down these temporary crosslinks – and replacing them with cured polyimides.
In the case of positive tone PSPI, the ester groups induce insolubility in the chosen developer. Irradiation causes the cleavage of the ester bonds resulting in a more soluble polyamic acid which is removed via development. The remaining unexposed PSPI-insoluble polyamic ester is then thermally converted into polyimides.
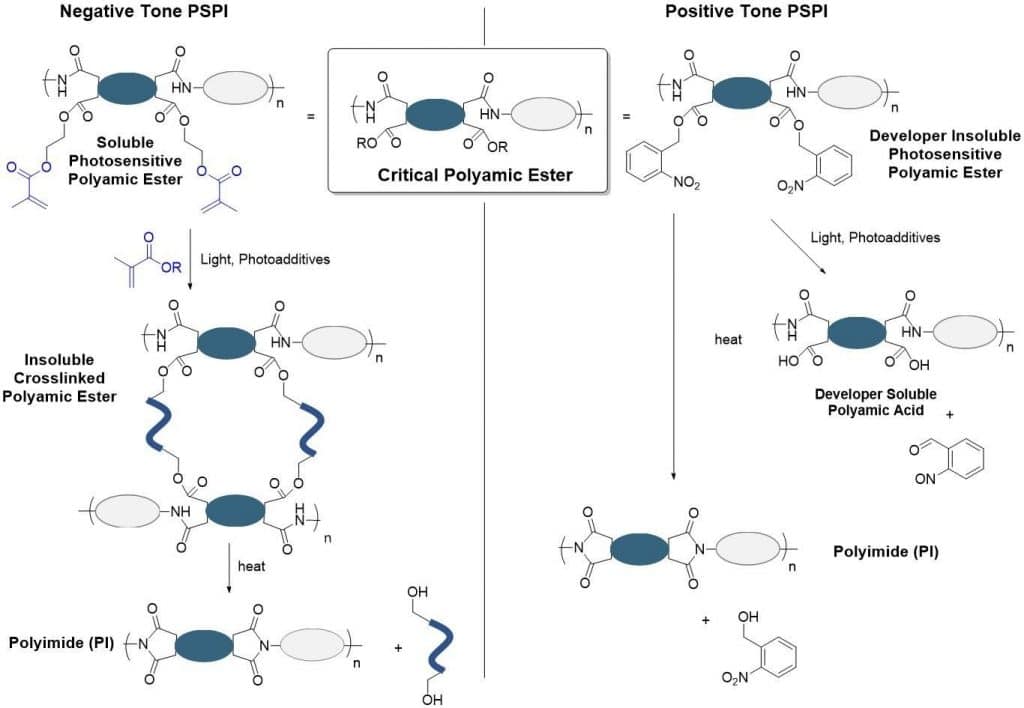
Figure 2. The working mechanism for Negative tone and Positive tone photosensitive polyimides. In each case, polyamic esters are the key structural intermediate leading to the final polyimide.
PSPIs are enabled through improved Polyamic Ester Synthesis Protocols
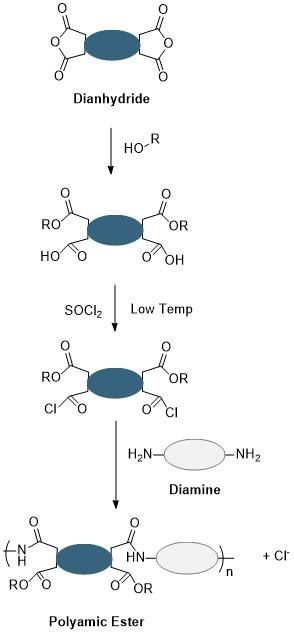
Given the importance of polyamic ester derivatives to the workings of photosensitive polyimides, reliable and efficient methods to synthesize polyamic esters are vital. Fortunately, the polyimide manufacturer has multiple synthetic routes to consider. An early developed route (Figure 3) involves first the reaction of dianhydride with alcohol to form a diester diacid compound. The carboxylic acids are reactivated in the subsequent step at low temperature with thionyl chloride to form acid chlorides. The activated acid chlorides then react with diamines to form the polyamic ester. While this route can afford the desired polyamic ester structure, it suffers from several complications, including:
- The necessity of performing the thionyl chloride reaction at reduced temperatures
- Generation of chloride ions in the final step which requires purification via ion exchange
- Reduced control of the polymerization step leading to highly polydisperse polyamic esters
Figure 3. Thionyl chloride route leading to polyamic esters which suffers from the required low temperatures and additional purification needed.
Halocarbon Isoimidization Processing Agents Enable more Efficient Synthesis of PSPIs
Motivated by the challenges of the thionyl chloride route for polyamic ester synthesis, Halocarbon Electronics Solutions worked with leaders in the industry to develop an alternative and simplified approach. This route does not generate byproducts upon formation of the ester and amide bonds of the polyamic ester, thus eliminating the need for costly post-polymerization purification. Moreover, control of the polymer molecular weight is enabled through controlled condensation polymerization strategies involving diamines and dianhydrides. This route has been realized using the polyisoimide as a reactive precursor that can be cleanly and easily transformed to the desired polyamic ester. Moreover, this polyisoimide can be generated easily and cleanly using Halocarbon Isoimidization Process Agents. Because the polyamic ester can be generated cleanly and without evolution of any byproducts from the reaction of polyisoimides and alcohols, the polyisoimide route is a preferred method to produce photosensitive polyimides.
Upon completion of the polyamic ester synthesis, the solid resin is precipitated with water and then washed extensively before drying. The purified resin is then be formulated into the final PSPI formulation for use in advanced electronic packaging applications.
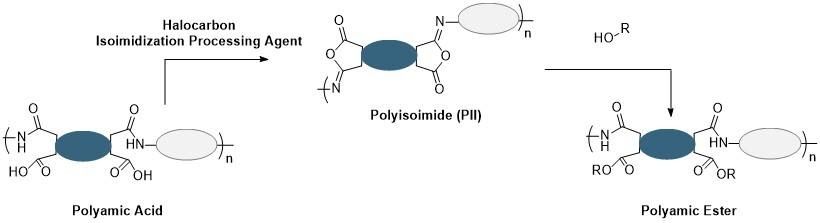
Figure 4. Polyisoimide route for the clean, simple, and efficient production of polyamic esters.
The Halocarbon Electronics Solutions Isoimidization Processing Agents are high purity, electronics-grade, process chemicals available in large quantities and high quality to enable the clean production of polyisoimides to produce photosensitive polyimides. As outlined above, the following benefits are provided with the use of Halocarbon Process Agent:
- Efficient production of PSPIs through the Polyisoimide intermediate leading to the Polyamic Ester precursor
- The clean production of Polyamic Esters without the generation of chloride ions or other byproducts
- Elimination of the need for reduced temperatures for the entire synthetic scheme
Semiconductor Packaging is driving More than Moore due in part to access to advanced materials made in efficient means. Halocarbon Electronics Solutions will continue to do our part to enable these vital materials.
Contact us to learn more about Halocarbon Electronic Solutions materials for the formation of photosensitive polyimides for electronic packaging or reach out directly to our sales manager.